From parchment to pigment
Natural materials in the archives
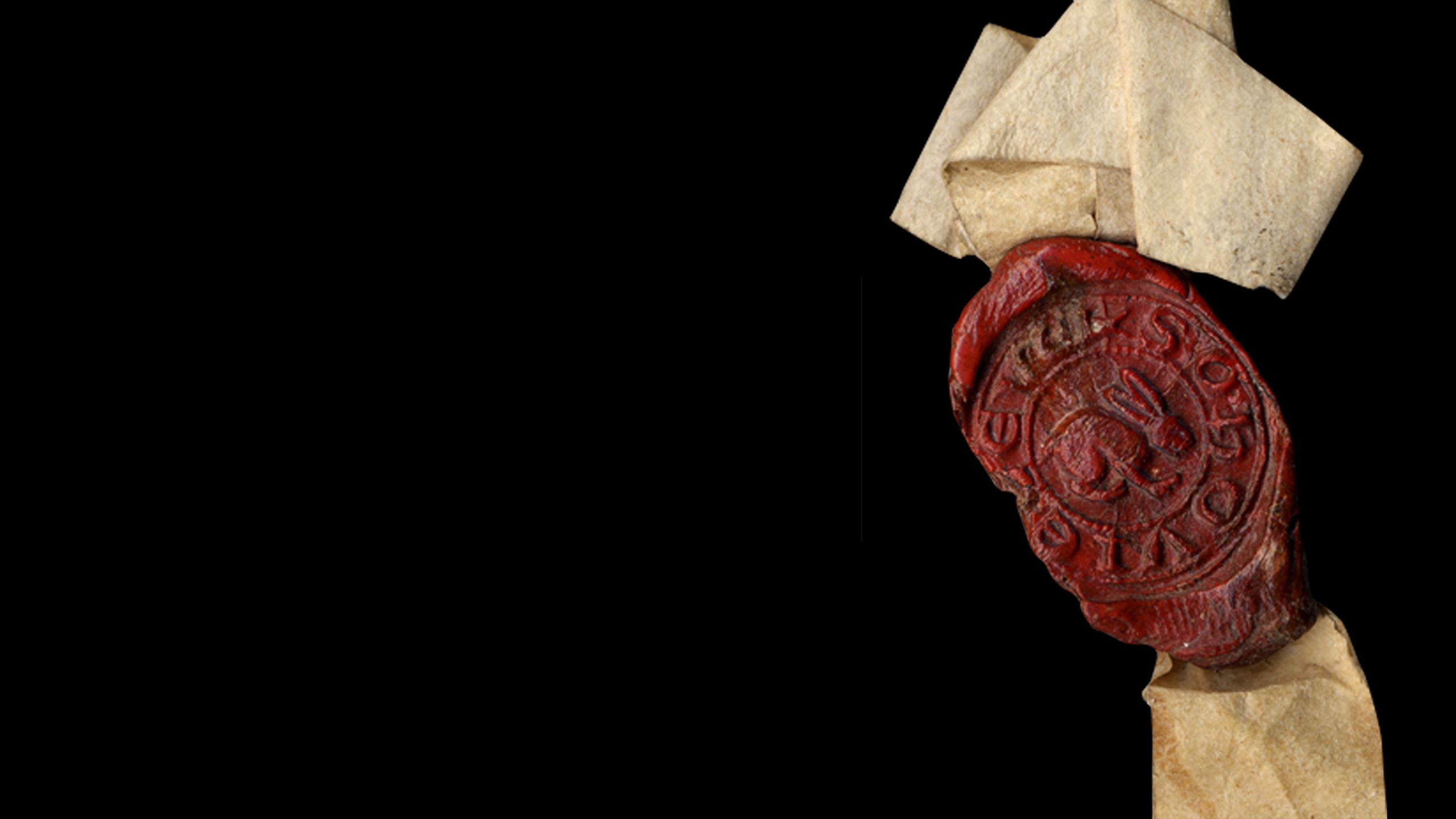
What are our archives actually made of?
From minerals and metals to plants and pulp, how did people in the past make all of the things that we look after in our collections today?
Parchment
The oldest document we care for in our collection is the Eye Charter, which dates from c.1119 (HD1538/7/f38). It is a royal charter issued by Henry I (a son of William the Conqueror) and granted rights to the monastery of St Peter in Eye.
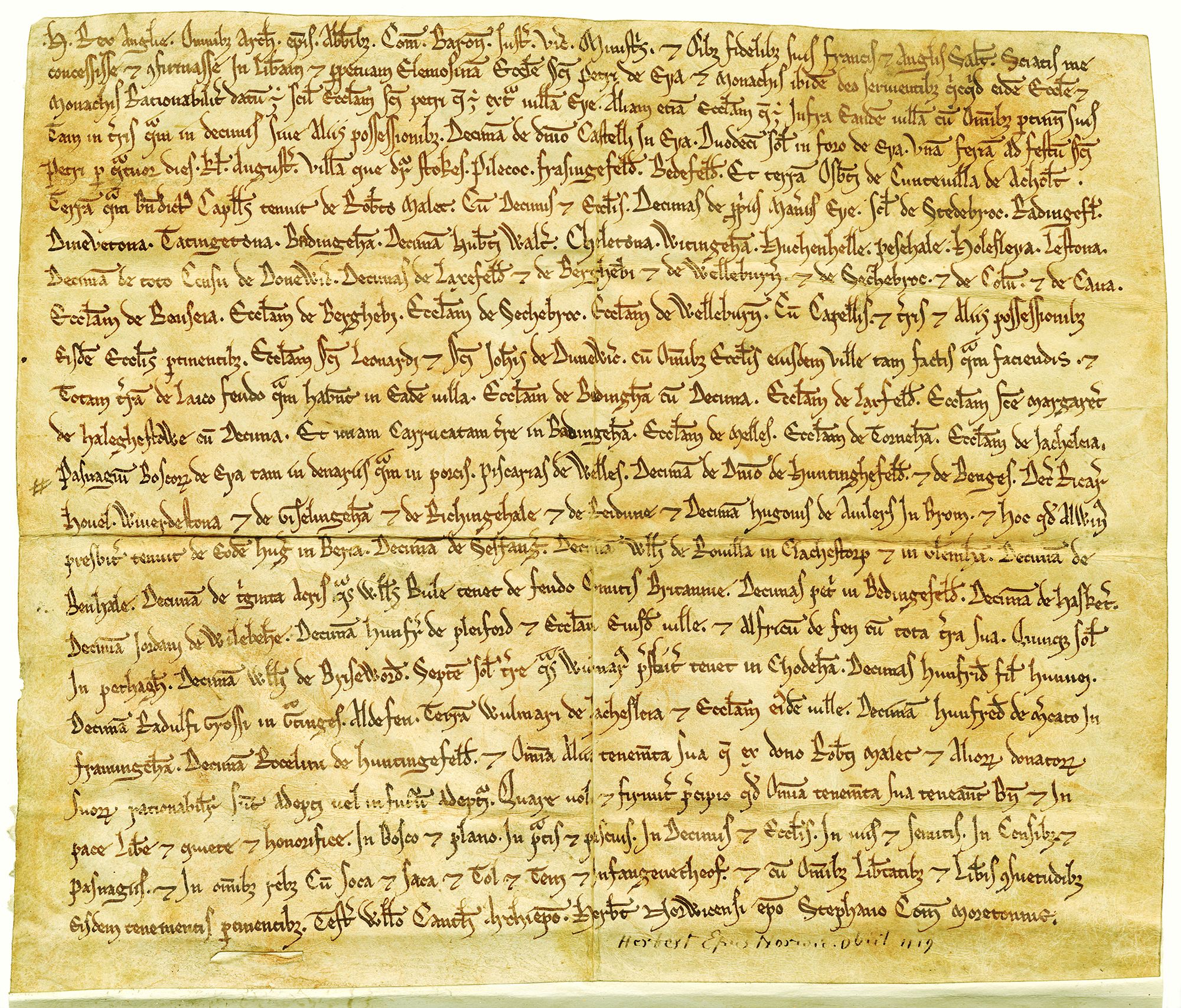
The charter is made from parchment, a writing material that has been in use for over 2,000 years. Parchment is made from animal skin, usually sheep, calf, or goat.
To make parchment the skins are first immersed in lime solution for 1-2 weeks to loosen excess material such as hair. After soaking, these layers were then removed by hand with special knives over a wooden sloped ‘beam’.
After most of the excess material had been removed the skins were stretched taut onto a frame and scraped with a half-moon shaped knife to stretch the skin and squeeze out unwanted substances. Hot water may be applied to help. When clean the skin was were stretched onto a frame so it would dry thin and taut. Once dry the skin could be shaved if more thinning was needed or to whiten the surface. Depending on its use the skin may also be coloured or have coatings applied, and after removal it may be smoothed with pumice. You can see how this process was still carried out in the twentieth century in the film below from British Pathe.
Parchment is very sensitive to its environment. If exposed to high humidity it becomes wrinkled and can become mouldy, and if kept in too dry an environment it becomes brittle.
Despite these risks, when stored properly parchment can last for an extremely long time – as shown by the survival of the Eye Charter. For this reason the British government still uses parchment to record new laws.
From the later Middle Ages parchment was gradually replaced by paper for most uses. Paper could be produced more cheaply and following the development of the printing press the production of parchment could not keep up with demand for materials.
Find out More:
William Cowley, the last parchment manufacturers in the UK
BBC ‘Domesday’ feature on William Cowley
Jesse Mayer, American parchment-maker
Just for fun:
Leather
These volumes are bound in two different types of leather. The darker leather on the left was ‘tanned’, while the leather on the right is alum-tawed. Tanning is still a widespread process today (although carried out using modern methods), but by the 19th century alum-tawed leather had limited use in items such as gloves.
Leather-making begins in the same way as parchment-making; an animal skin is soaked in water, then in a solution of lime, and then scraped to remove hair and flesh. The skin might then be treated in solutions of enzymes or fermenting barley, rye or other plants to further loosen it. As these were smelly and unpleasant treatments (even including dog dung or bird droppings!), processing yards were often required to locate on the edges or outside towns. Thus ‘Tanners View’ in Ipswich, for example, is some way from the town centre and adjacent to the River Gipping from where the necessary water supply was taken.
Tanning a skin makes it durable and water resistant. In the traditional English tanning process skins were soaked in a solution of water and crushed oak bark, then layered with ground oak bark, and left for up to a year. At the end of the process the skins would be rinsed and left to dry slowly, before a final stretching and scraping and an application of grease.
Alum-tawed leathers were processed by ‘whittawyers’ and later glovers. Skins were treated to remove hair, flesh and were loosened up in the same way as tanned leathers. Then a paste of alum mixed with other materials like salt, egg yolks, butter, oatmeal or flour, and vegetable oils was worked into the skin for a few hours by kneading or trampling on it in a tub. The skin was dried, re-worked the next day if needed and finally made flexible by working it back and forth over a thin edge. It was a messy and hard job but the end result was worth it: a bright white, smooth, flexible, and supple leather.
Of parchment and these two leathers only the tanned leather is permanently resistant to decay: the preservatives in parchment or alum-tawed leather can be washed out so reverting to a raw skin which will putrefy if wet or shrink and dry to resemble a dog chew if dried; in either case they become useless. Tanned leather meanwhile can last for centuries either wet or dry.
To be used in bookbinding the edges of a piece of leather are pared with a knife to thin them, to make neat edges and corners. To create the book covers, the leather was then wrapped around a wooden panel – in England usually oak, but sometimes beech. The holes we can see in the ‘Black Domesday’ binding today are likely from woodworm.
Find out more:
Video from J & FJ Baker, the last oak tanners in Britain, on the tanning process
Museum of Leathercraft, Northampton
A history of the bookbinding industry in Tudor London, in the Victoria County History for Middlesex
Paper
This will is one of many thousands of documents we look after which are made of paper.
For the first three to four centuries of papermaking in Britain foreign imports and recycling were central to the trade. By the time the first papermill was established in England by John Tate near Hertford in the 1490s papermaking had already been established in other European countries for between 100 and 300 years. Thus our earliest writing papers in the archives must have been imported, and as papermaking was a difficult business to establish and make profitable foreign imports for certain papers continued into the 1800s.
Modern paper is generally made from wood pulp, but this process was not developed until the 1840s. Before this, paper was generally made from recycled textiles. By the time textiles came to be used to make paper, they would already have had a long life, perhaps as clothing or sailcloth or rope. Clothes were some of the most valuable things people could own, and they would be repaired, altered, and passed down until they had completely fallen apart, when they would be sold as rags.
In Britain a great deal of clothing was made from linen (made from the fibres of the flax plant) and from the late 1700s cotton. Rags from these garments were used to make higher quality white writing paper.
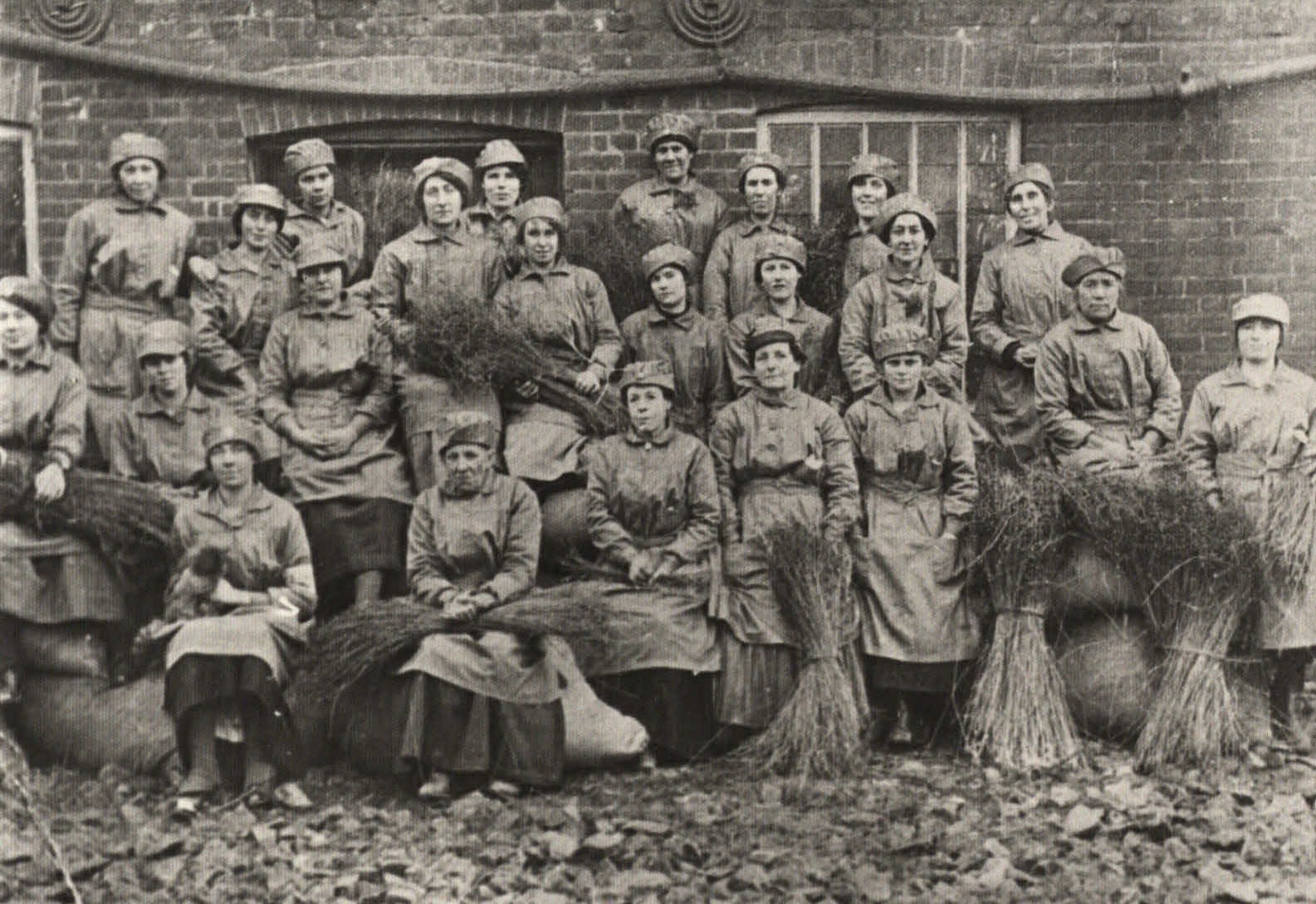
Workers at a flax factory in Glemsford, c.1914-1925. Flax production in the area was controlled by the government during the First World War, to ensure a supply of linen for the war effort (K681/1/184/33)
Workers at a flax factory in Glemsford, c.1914-1925. Flax production in the area was controlled by the government during the First World War, to ensure a supply of linen for the war effort (K681/1/184/33)
Coarser textiles and cordage made from hemp such as such as sailcloth and rope were used to make brown utility papers (for general wrapping, book covers, wall and furniture lining, etc.). It was easier to make the coarse brown papers and papermaking in Suffolk is likely to have been in this style, especially with the plentiful local supply of old maritime ropes and canvas.
To make paper before the 19th century, the rags were fermented (‘retting’) and then chopped up, and anything that wasn’t useful fibre removed (such as buttons and pins). The rags were then beaten to break them down into a pulp. The pulp was mixed with water in vats, formed into sheets on papermakers moulds, pressed, and dried. Finally if needed the sheets were ‘sized’ to make them water-resistant and stronger.
Find out more:
- Paper History in Britain, from the Association of the British Association of Paper Historians
- Playlist of videos of paper making
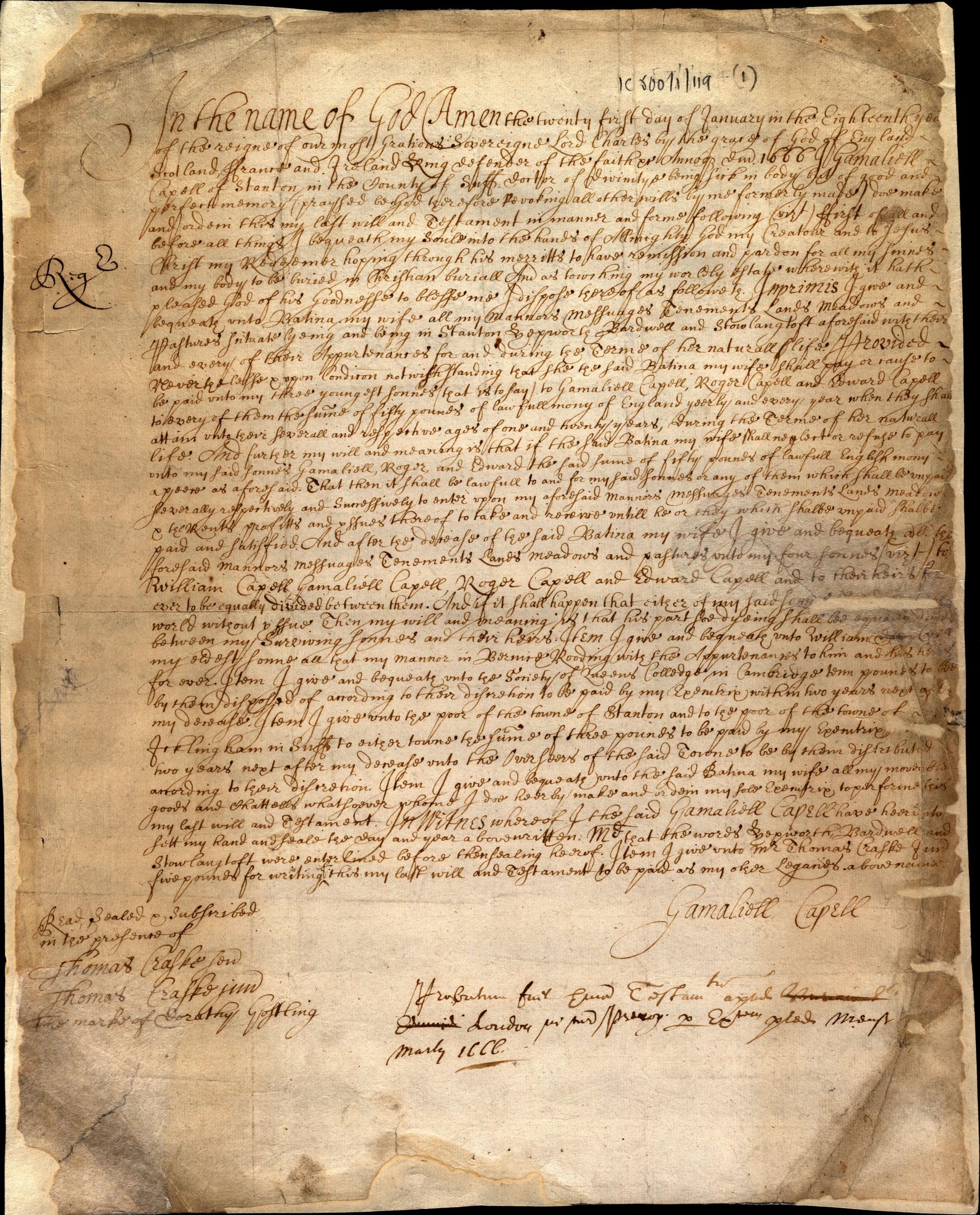
Wax seals
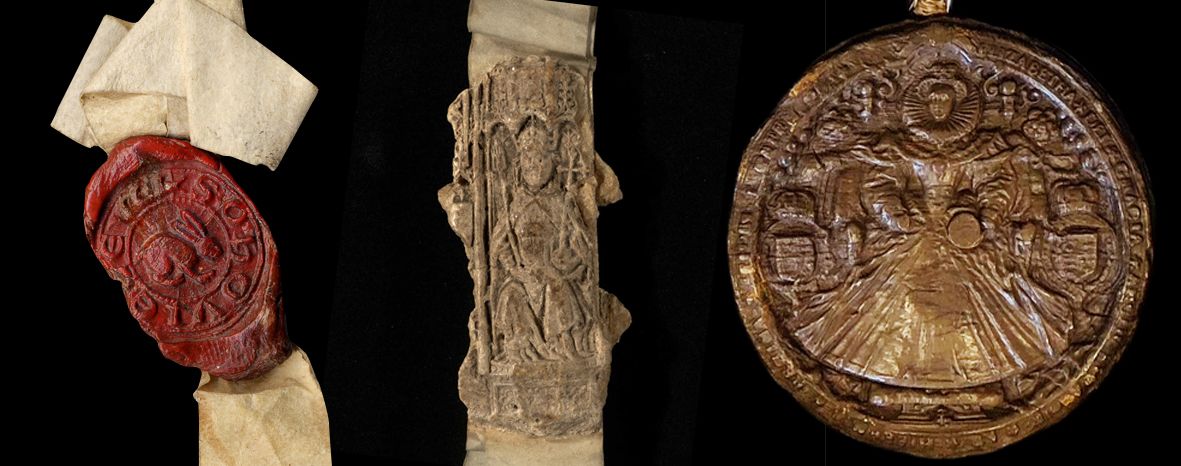
Seal with a hare motif attached to a document of 1340, arranging the lease of land in Flixton (741/HA12/B2/3/29); Fragments of a Great Seal of Henry VIII, 1510 (741/HA12/B1/1/3); Great seal of Elizabeth, 1587 (HA528/30)
Seal with a hare motif attached to a document of 1340, arranging the lease of land in Flixton (741/HA12/B2/3/29); Fragments of a Great Seal of Henry VIII, 1510 (741/HA12/B1/1/3); Great seal of Elizabeth, 1587 (HA528/30)
Medieval seals generally made with beeswax and resin extracted from larch trees, coloured red with vermilion (made from cinnabar, the ore of mercury). Beeswax is produced by honey bees, who use it to built honeycomb cells.
From the 16th C sealing wax was made from a mixture of shellac, turpentine, resin, and chalk or plaster, and colouring (vermilion or red lead). Shellac is made by processing the resin secreted by female lac bugs. These tiny insects are parasitic on certain trees, which are found particularly in India and Thailand. They suck up sap out of the tree, and exude it back out in a chemically altered state as a resin. The crusty resin is processed and broken up into flakes, which can then be dissolved in alcohol to make a liquid.
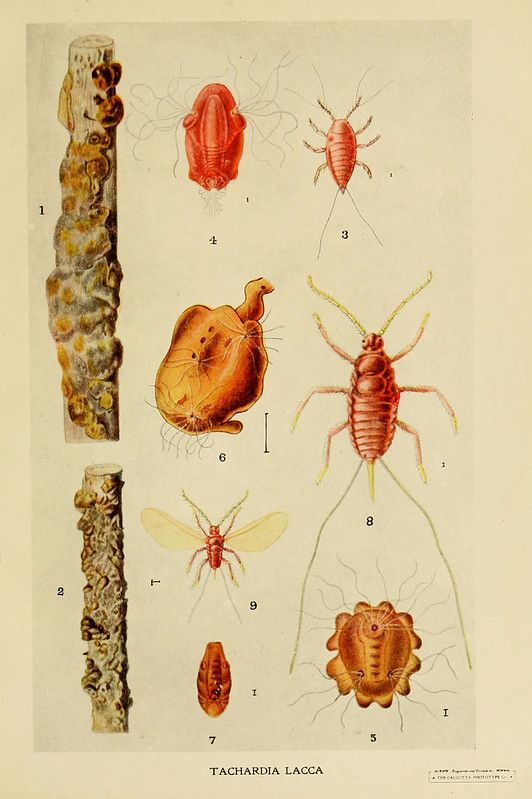
Indian Insect Life, Calcutta ;Thacker, Spink & Co., W. Thacker & Co., 2 Creed Lane, London, 1909, from the Biodiversity Heritage Library on Flickr
Indian Insect Life, Calcutta ;Thacker, Spink & Co., W. Thacker & Co., 2 Creed Lane, London, 1909, from the Biodiversity Heritage Library on Flickr
Ink
The ink most commonly used across Europe between the 5th and 19th centuries was iron gall ink. This purple-brown or black-brown ink is made by combining three main ingredients:
- Oak galls – bulbous growths that occur on oak trees as a result of parasite attack, which contain a high level of tannins
- Iron sulphate (in the form of copperas, a blue-green, crystalline mineral – made in a very hazardous process by allowing iron pyrite to decompose and then heating it)
- Gum Arabic – made from sap from Acacia trees
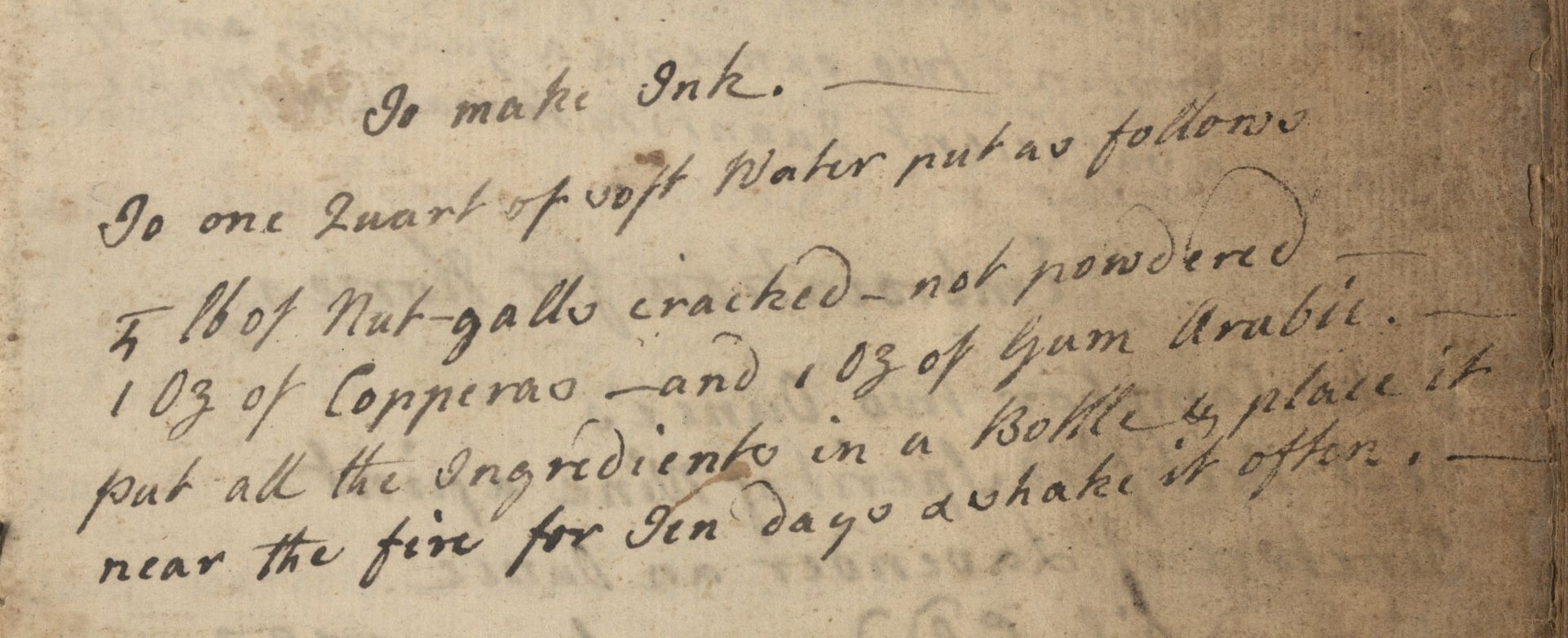
Recipe for iron gall ink from recipe book of Susan Farr, 1775-1804 (1150/2/F/2/48)To make Ink. To one Quart of soft Water put as follows¼ lb of Nut-galls cracked – not powdered1 oz of Copperas – and 1 oz of Gum ArabicPut all the ingredients in a Bottle & place it near the fire for ten days & shake it often
Recipe for iron gall ink from recipe book of Susan Farr, 1775-1804 (1150/2/F/2/48)To make Ink. To one Quart of soft Water put as follows¼ lb of Nut-galls cracked – not powdered1 oz of Copperas – and 1 oz of Gum ArabicPut all the ingredients in a Bottle & place it near the fire for ten days & shake it often
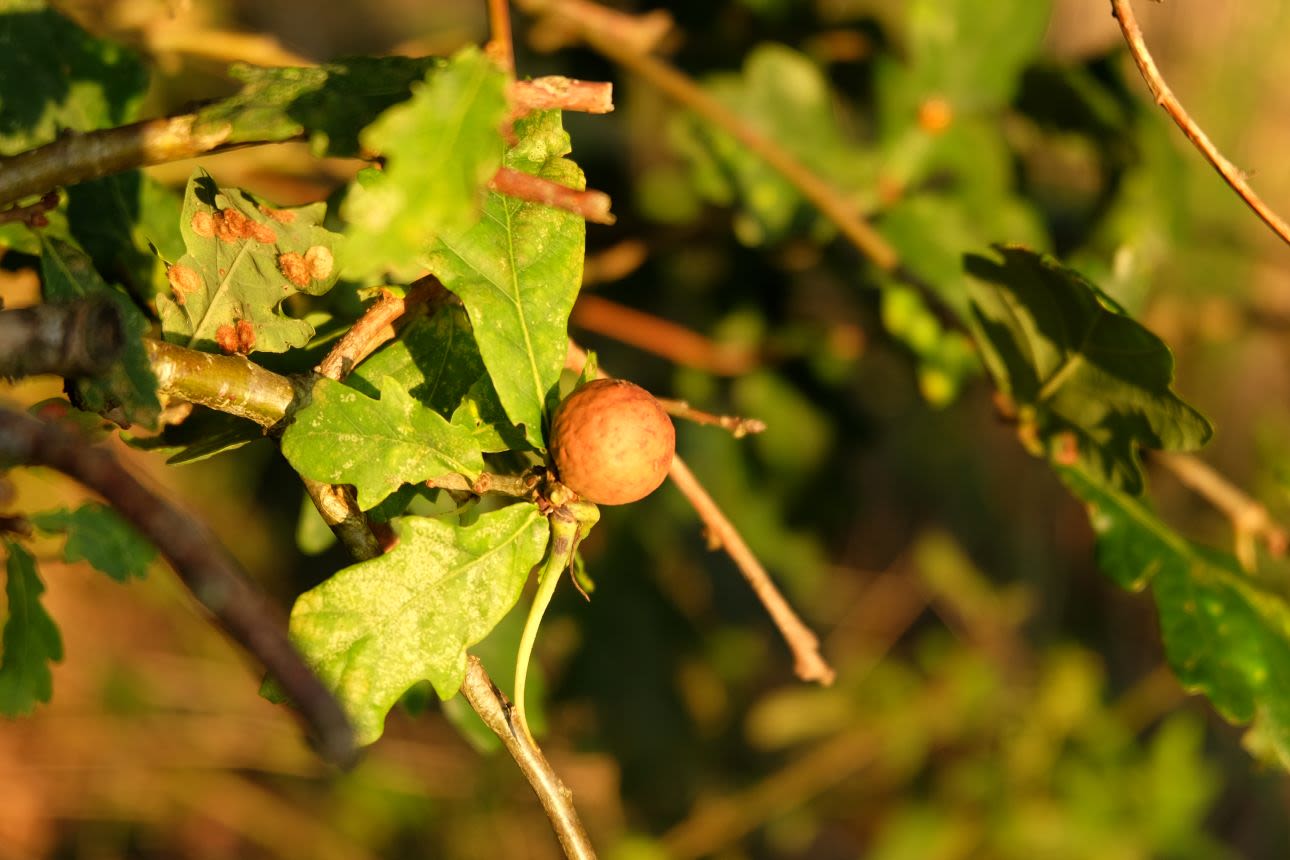
An oak gall
An oak gall
These ingredients were widely available and produced an indelible ink which could not be smudged or washed away with water.
When conserving documents written with iron gall ink on linen-based paper water can be used to wash away years of dirt and refresh the bonds between the fibres in the paper.
Iron gall ink does, however, present conservation challenges. The ink is acidic, and over time can eat through the surface it was used on, leaving holes where the writing once was.
Find out more:
Pencil
Documents written in pencil occur frequently in our collections. The substance within pencils which leaves a mark on the writing surface is graphite – a crystalline form of carbon.
The earliest pencils were made using solid graphite, wrapped in string or sheepskin. This graphite came from a large deposit that was found in 1564 in Cumbria, which could be sawn into sticks. This remains the only large-scale deposit of its type ever found.
Today most pencil cores are not made of solid graphite but of graphite powder mixed with a clay binder, a technique that was developed in the 17th century.
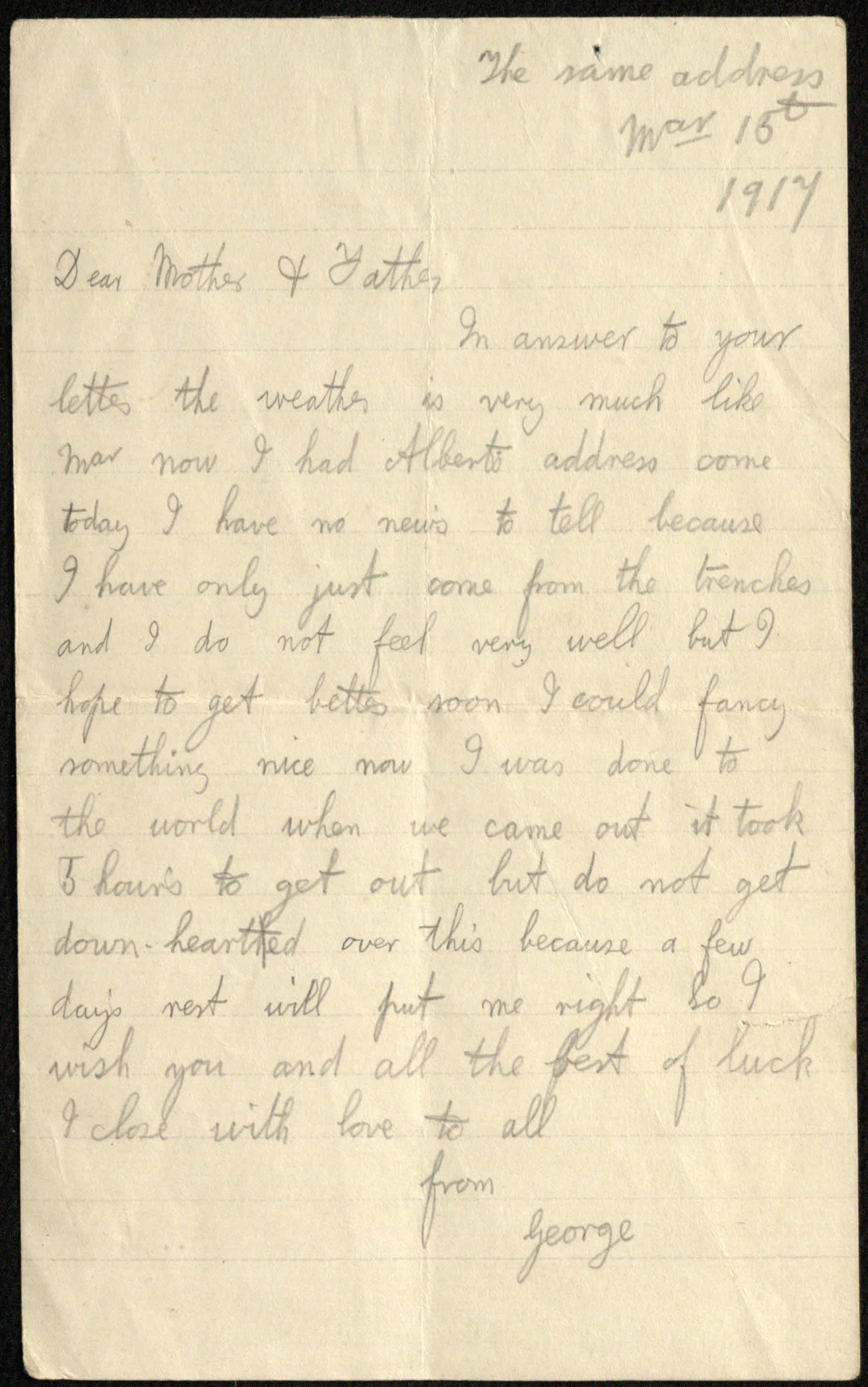
Letter written in pencil by George Stopher during the First World War to his parents at home in Sweffling, 15 Mar 1917 (HD825/2/217)
Letter written in pencil by George Stopher during the First World War to his parents at home in Sweffling, 15 Mar 1917 (HD825/2/217)
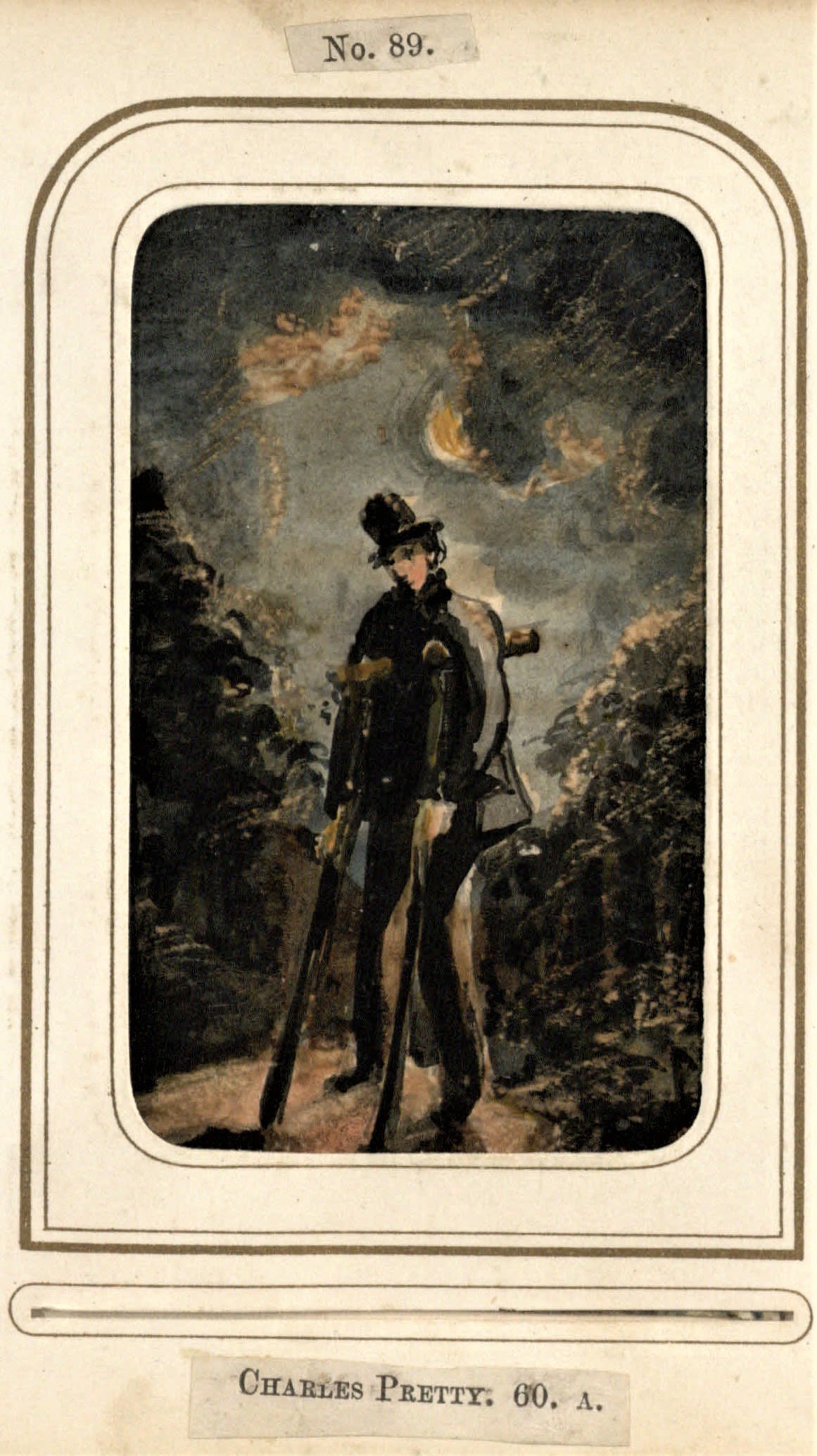
A watercolour of Charles Pretty of Wortham, from Rev. Richard Cobbold’s ‘An English Parish Poor Book’, 1862, which contains miniature portraits of a number of his parishioners (HD1025/2)
A watercolour of Charles Pretty of Wortham, from Rev. Richard Cobbold’s ‘An English Parish Poor Book’, 1862, which contains miniature portraits of a number of his parishioners (HD1025/2)
Pigment
Painting in the nineteenth century, the Rev. Richard Cobbold would have had access to some synthetic pigments, but many paints would still have been made using natural materials.
For most of human history painters had to make their own paints. Small, hard cakes of soluble watercolour were available to buy from the late eighteenth century, and by the time Rev. Cobbold was painting in the mid-nineteenth century paint boxes containing a selection of ready-made watercolours were available.
Colours available to Rev. Cobbold would have included those made from earth pigments, such as ochre, sienna, and umber. These are pigments made from naturally occurring minerals which contain metal oxides, mainly iron oxides and manganese oxides.
Metal oxides also featured in more recently developed pigments. Cobalt blue, made by heating cobalt oxide with aluminium oxide, was commercially available from 1803. It was a much cheaper alternative to ultramarine blue, which is made by grinding the semi-precious stone lapis lazuli.
Animal products also feature in historical paint pigments. Sepia was made using cuttlefish or octopus ink, and carmine red using the cochineal scale insect.
The tools Rev. Cobbold would have used to apply his paints and the surfaces he worked on would also have been made of natural materials; brushes were made from animal hair and wooden handles, and paper might be coated in animal glue or egg to prepare it for painting.
Silver
The daguerreotype process was invented by French artist and inventor Louis Daguerre and launched publicly in 1839. It was the first process that could not only create a photographic image but fix it so it was long-lasting. Having your portrait captured in a daguerreotype was hugely popular in the 1840s and 1850s.
The images were made on highly polished silver-plated copper sheets. These sheets were coated with light-sensitive iodine vapour and placed in a camera to be exposed, usually for several seconds. The plate would be removed from the camera and exposed to mercury vapour, then rinsed.
The process created one-off images on the surface of the silver-plated sheets; they could not be used to make multiple prints or copies as later techniques would allow. The finished images were easily damaged and sealed in small cases behind glass to protect them.
Find out more
https://www.youtube.com/watch?v=DAPgdo5H7ZY
Glass
The magic lantern was an early type of projector, used to astonish and entertain audiences with luminous, larger than life images.
These images were projected using transparent glass plates, initially hand-painted, and later with photographic images.
The slides were made of a layer of glass coated in a photographic emulsion, then another thinner layer of glass on top. The glass and emulsion sandwich is held together with tape all around its edge.
Glass is mostly made of sand, heated until it turns to liquid (at 1700 degrees C). Being made of glass, these slides are of course very fragile and need careful storage and handling.
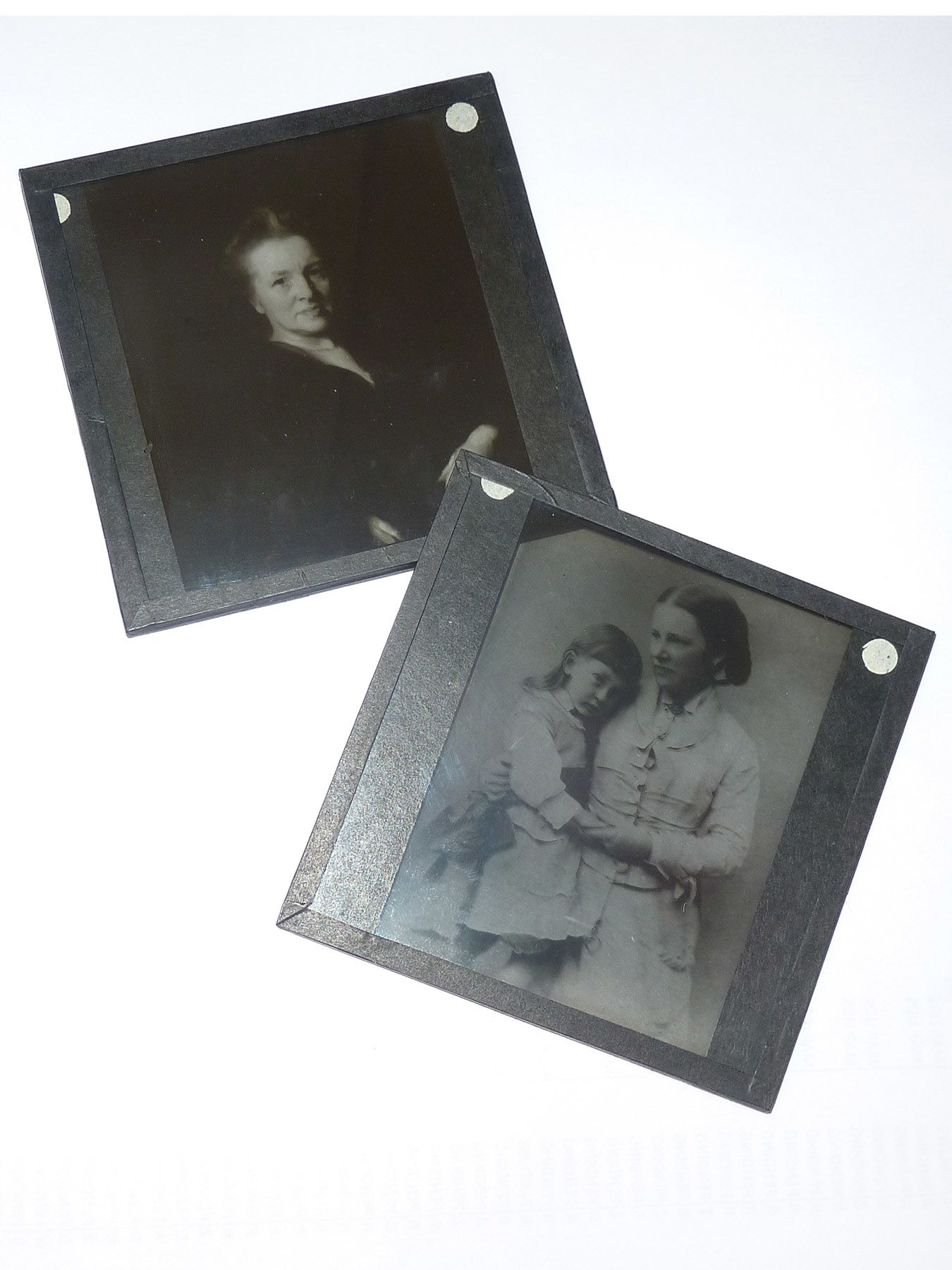
Glass lantern slides from the Garrett family collection. The bottom slide shows Elizabeth Garrett Anderson and her daughter Louisa, 1876 (HA436/4/2/1)
Glass lantern slides from the Garrett family collection. The bottom slide shows Elizabeth Garrett Anderson and her daughter Louisa, 1876 (HA436/4/2/1)